When is Custom Dip Molding Needed?
When is Custom Dip Molding Needed?
Do you need a cost effective way to protect personnel from bump hazards on shelving or other overhead devices?
In many cases, Harman Corp. can use our custom dip molding process to produce unique parts for added safety measures on operational machinery. We specifically use your exact substrate to configure molds for your application, preventing you from having to buy all new machinery, ultimately saving your business time and money.
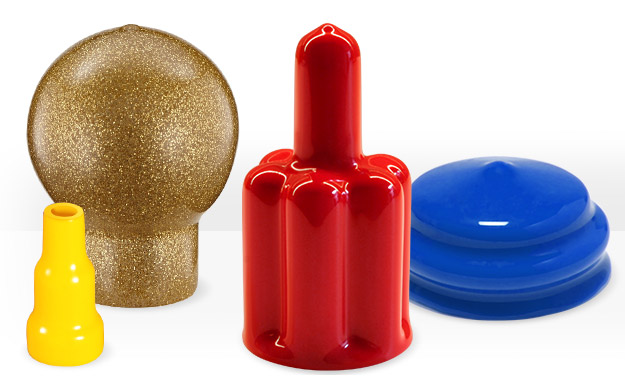
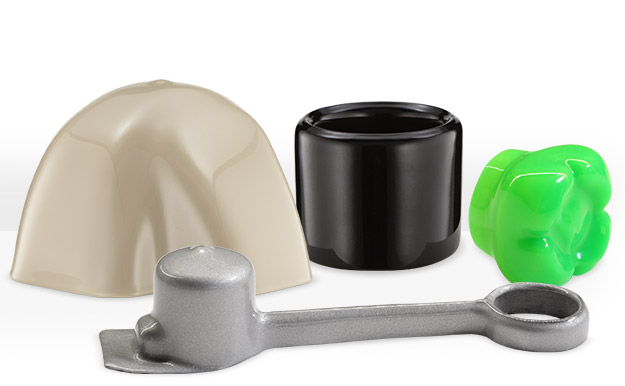
Will your plastic cap, grip or safety cover withstand extreme outdoor conditions?
Upon request, Harman can formulate material with a UV additive to guard against harsh effects from the sun on PVC products, preventing premature damage.
Are you in need of a quick turnaround on a concept-to-finished product?
In many cases, our custom dip molding services offer expedited turnaround times on custom plastic parts, allowing us to turn out thousands of concept parts in a manner of a few weeks.
Unable to use adhesive in your process for lack of bonding or it adversely affects your process?
Dip molded products are often molded so that a stretch is required to hold part securely, or in some cases part can be molded to use an attribute on the substrate to secure component.
Will you need a cap, grip or cover to fit a slightly irregular shape or does the size very part to part?
Not a problem. Our custom dip molding services use Flexible PVC (Plastisol) as our base polymer, which can be molded under the size and the stretchable nature of this product will accommodate irregular size or shape.
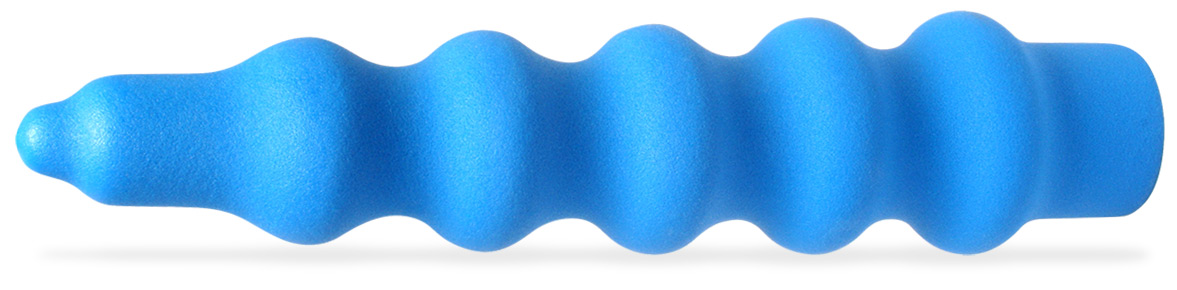
Looking for a custom plastic part for a specific application?
Learn more about our Custom Dip Molding services, or call us directly at